The Problem
Our client was alarmed that the refinery was using substantially more energy than it was designed for. Its land-locked location, with no access to natural gas, makes it reliant on expensive liquid fuels.
The refinery processes 200 KBD of heavy crude to match its coking configuration. It also combines a mild hydrocracker with deep conversion fluid cat cracking to maximise the production of propylene. With limited power available from the local grid, the refinery has its own captive power plant producing more than 100 MW and 600 T/h steam. A third of this is used by condensing steam turbines to drive the large process machinery, including wet gas compressors, with a total shaft work of 40 MW.
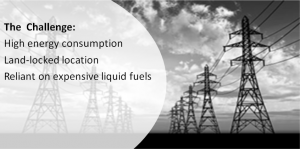
Our approach
The client commissioned us to perform our Energy Plus programme, which involved three main activities:

Our rigorous analysis established the energy-efficiency of the process facilities with optimal heat recovery, so the often recommended "Pinch Analysis" could not identify any significant energy performance opportunities.
We found three energy performance shortfalls in the process units.
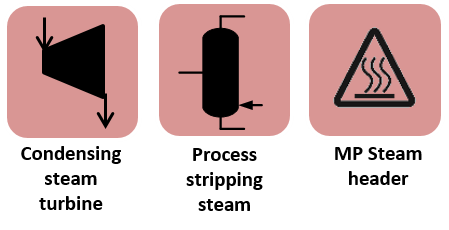
The largest occurs in the condensing steam turbines which have an overall cycle efficiency of only 25%. This means that 160 MW of site fuel is needed to deliver the 40 MW of power to the processing units, losing 120 MW to the cooling medium.
Secondly, the process area uses medium pressure steam (MPS) for process stripping, instead of the standard low pressure steam (LPS). As a result, the back pressure turbine supplying the steam has to generate more power. Compounding this, the turbine supplying MPS is much less energy efficient than the LPS turbine.
In addition, because the MP header is held at a higher pressure than it needs to be, the power produced from the MPS turbine is reduced.
The 'Plus' part of the programme identified ways of increasing the refinery's gross margin that would work in synergy with the improvements in energy performance. Our engineers found ways of increasing yield by USD 82 million a year - a third of which could be achieved through operational changes without capital investment. The refinery has already implemented one of these improvements, worth an estimated USD 12 million a year.
Outcome
Reducing the pressure of the MP header by 1 bar would generate an additional 0.5 MW of electric power, saving USD 1 million a year in site fuel. This change is easily implemented and requires no investment.
Converting the stripping steam piping and control valves to use LPS, instead of MPS, and transferring the steam load from the MP extraction turbine to the LP back pressure turbine will generate an extra 7 MW of electric power, providing an annual site fuel saving of USD 10 million. Achieving this would require a minor investment, preparatory engineering and a shutdown of the plant.
Finally, our Energy Plus programme showed that if the refinery were to invest in converting the condensing steam turbine drivers to electric motors, it could potentially save USD 45 million a year in site fuel. However this would mean extensive reworking and site closure and could therefore not be recommended. However this realisation does serve as a benchmark strategy for any future energy system configuration.
